Negli ultimi anni, molte ricerche e studi hanno sottolineato quanto la digitalizzazione e l’innovazione data-driven siano lo strumento principe per sostenere la crescita delle aziende e garantire un vantaggio competitivo nel mercato. La conseguente grande attenzione agli investimenti in digitalizzazione, riservata dall’Unione Europea nelle indicazioni di applicazione dei PNRR nazionali, ha avuto in effetti un discreto impatto, come emerge nei risultati del Digital Economy and Society Index (DESI) 2022 della Commissione europea.
Lo studio mostra, però, quanto sia ancora indietro il livello di adozione di tecnologie digitali fondamentali per lavorare su processi e ottimizzazioni concrete, come per esempio l’adozione di strumenti di intelligenza artificiale e analisi di Big data.
La sfida della digitalizzazione dei dati di processo
In particolare, il manifatturiero e le piccole e medie imprese mostrano la prima grande incongruenza: benché ben il 72% delle aziende manifatturiere raccolga dati di processo, il 15% di queste aziende in Europa non li analizza in alcun modo e quasi il 40% fa solamente analisi ex-post. Benché la mancanza di competenze interne sia portata come spiegazione di questo ritardo, diventa evidente che a questa si aggiunge una mancanza di visione.
I migliori progetti industry4.0, che hanno portato concreto valore aggiunto allo sviluppo e alla crescita aziendale, sono infatti quelli nati da una visione. Questo è il caso di Fedrigoni, guidata dalla consapevolezza che la gestione coerente e organizzata dell’insieme degli stabilimenti, attraverso l’analisi dati gli avrebbe consentito di ottimizzare la produzione. Questo pensiero ha portato l’azienda a realizzare un progetto titanico di trasformazione digitale del sistema di controllo di processo.
Il caso Fedrigoni
Attraverso la personalizzazione del prodotto, Kode ha creato per Fedrigoni uno strumento che consente di monitorare l’efficienza delle macchine continue di tutti gli impianti. L’obiettivo era di dare al management aziendale uno strumento rispettivamente operativo e strategico per ottimizzare la produzione di ogni specifico impianto e allo stesso tempo confrontare l’andamento complessivo di tutti gli impianti.
Il progetto nasce quindi dall’esigenza di digitalizzare, storicizzare e uniformare i dati provenienti da impianti diversi per ottimizzare il controllo delle performance di produzione. Questo progetto è stato realizzato attraverso 2 fasi principali:
- Data Management Module: composto da una fase esplorativa di analisi e comprensione di tutte le fonti dei dati (sostenuta da un importante lavoro di pre-processing)
- OEE Module: l’implementazione di algoritmi in grado di misurare tutti gli aspetti degli indicatori chiave richiesti per la costruzione di dashboard uniformi per tutti gli impianti.
Ottimizzazione e controllo: le peculiarità della produzione di Fedrigoni
Fedrigoni ha oltre 70 centri di produzione, taglio e distribuzione, in cui nascono migliaia di tipologie di carte speciali, etichette e materiali autoadesivi. Alcuni dei suoi impianti alternano la produzione di tante SKU, mentre altri sono focalizzati su pochi specifici prodotti, mostrando conseguentemente un rapporto fra produzione e scarto molto diversi fra un impianto e l’altro. Già questo aspetto rende difficilmente comparabili i dati di produzione degli impianti.
In aggiunta, va considerato che, in casi come quelli della produzione di carta, ogni macchinario ha dimensioni comparabili a un intero impianto produttivo, la cui costruzione ha di conseguenza, specifiche complessità. Ognuno di essi è perciò dotato di sistemi integrati di registrazione dei dati di processo molto differenti, tanto in termini di scala, che di frequenza di estrazione. Ad esempio, dal momento che, per comprendere in uno sguardo l’andamento dell’intera produzione, l’esigenza di Fedrigoni era di poter confrontare in maniera stabile alcuni indicatori chiave (dalla quantità prodotta, alle tempistiche di produzione, allo scarto generato), il problema si amplifica nel momento in cui il confronto deve essere fatto con macchinari che non estraggono del tutto uno di questi indicatori.
Rendere comparabili i dati di più stabilimenti
Il bisogno di rendere comparabili i dati di più stabilimenti è stata quindi un’esigenza fondamentale, che ha portato a scegliere di utilizzare i tag di macchina per poter ricostruire dai segnali di base della produzione (puntuali e inconfutabili) tutti i calcoli dei KPI selezionati in maniera uniforme. Il progetto, nato con pochi stabilimenti come test si è velocemente evoluto fino a coinvolgere 7 impianti in tutta Italia e 13 macchinari diversi in soli 3 anni.
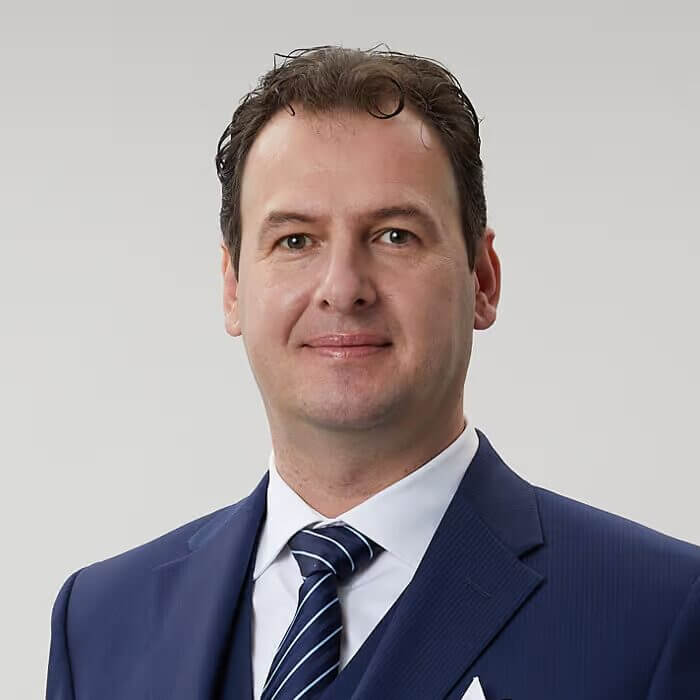
“Fedrigoni, negli ultimi 4 anni, ha intrapreso un percorso di trasformazione significativo che ha portato il gruppo a raddoppiare il proprio fatturato, triplicare l’Ebitda e acquisire 15 aziende in tutto il mondo (dalla Cina, agli Stati Uniti). Oggi produciamo 25.000 prodotti distribuiti a oltre 30.000 clienti in 132 paesi. Un’accelerazione della crescita così spinta porta con sé un’enorme complessità, che senza l’aiuto di piattaforme di Big data, difficilmente avremmo potuto governare. La collaborazione con il nostro partner Kode ci ha permesso di ottimizzare la produzione dei singoli impianti e di confrontare al contempo le performance dei diversi siti produttivi tra loro, favorendo il nostro processo di miglioramento continuo”, dichiara Gionata Berna, Chief Information Officer, Fedrigoni Group.
Il data management module: l’integrazione dei Big data
Ogni stabilimento espone molte migliaia di segnali di macchina; per ciascuno sono stati identificati insieme a Fedrigoni i tag da analizzare in dettaglio e di ciascuno è stata verificata la ricezione, la frequenza e il significato nel processo produttivo. Ciascuno di essi è stato sottoposto a un processo di storicizzazione e confronto con i dati esposti dal sistema di analisi integrato di ogni macchinario.
Tutte queste tappe hanno consentito di verificare la disponibilità dei dati necessari per applicare gli algoritmi di calcolo degli indicatori richiesti per il monitoraggio della performance di tutti gli impianti coinvolti.
La successiva fase di nomenclatura, pulizia e normalizzazione di questi Big data ha consentito di strutturare un database unico in grado di offrire una visione omogenea dell’insieme della produzione.
L’esigenza di Fedrigoni non si esauriva nella visione d’insieme, ovviamente, quindi il sistema è stato strutturato per consentire approfondimenti, non solo su base temporale, ma anche per tipo di prodotto, arrivando a distinguere fra i diversi tempi di fermo.
La piattaforma è stata, quindi, integrata della possibilità di inserire dati specifici di produzione, come la SKU, la grammatura della carta specifica per ogni produzione, la motivazione del fermo e molti altri, creando un sistema che integra i dettagli della macchina e la capacità di comprensione del reale degli operatori, per una visione e interpretazione utile alle scelte strategiche dell’azienda.
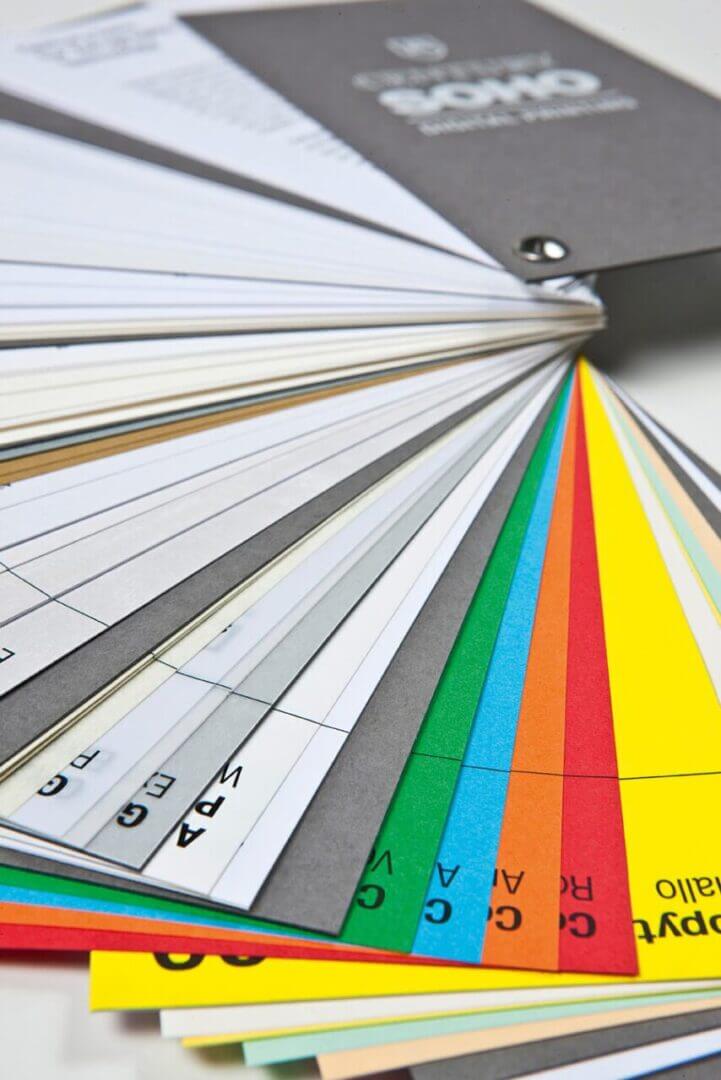
Il modulo OEE: il controllo delle performance
Per l’effettivo monitoraggio delle performance produttive del processo, si è proceduto con l’implementazione e la customizzazione del modulo OEE di FactorAI, per calcolare gli indicatori fondamentali per il monitoraggio:
- efficienza tempo: la percentuale di tempo produttivo rispetto al totale (availability)
- efficienza materiale: la percentuale di prodotto buono rispetto al totale (quality)
- efficienza velocità: il rapporto tra la velocità di produzione e la velocità teorica (performance)
- OEE: indicatore di sintesi dei tre precedenti che permette di esprimere con un unico KPI le performance del macchinario sotto monitoraggio.
Per Fedrigoni si è anche provveduto a integrare una customizzazione ad hoc che prevede una fase di aggregazione e segmentazione dei dati continui forniti dai tag di macchina in dati per bobina, in modo da poter attribuire puntualmente le performance OEE alla singola bobina prodotta dal macchinario.
I KPI e i dati così calcolati sono stati messi a disposizione degli utilizzatori finali, dirigenti di impianto e direzione aziendale, tramite una dashboard interattiva di real-time monitoring.
La dashboard fornisce il massimo livello di interazione con il dato di performance, permettendo al plant manager di effettuare analisi a diversi livelli di aggregazione temporale, con visioni annuali, mensili e giornaliere e dettagli a livello di prodotto, inviando in aggiunta, automaticamente, report di sintesi mensile con le informazioni salienti per la direzione aziendale, fornendo così una visione di sintesi delle performance dei singoli stabilimenti.
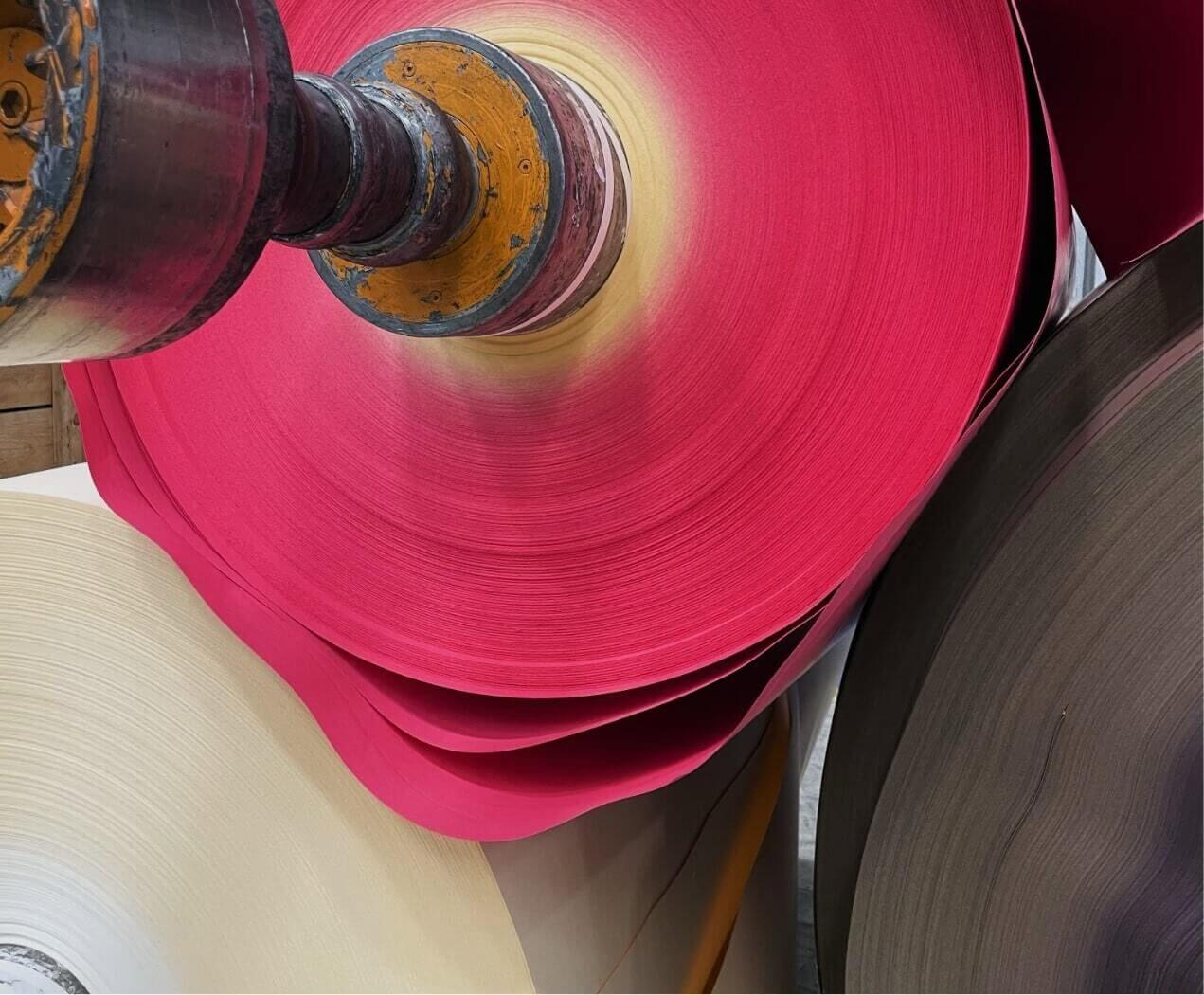
Gli effetti del monitoraggio dell’OEE con l’aumento della produzione
L’Overall Equipment Effectiveness è un indicatore che richiede monitoraggio continuo, soprattutto in aziende in cui la produzione è in crescita. L’aumento della produzione può infatti comportare importanti oscillazioni sugli scarti e sull’efficienza tempo.
Grazie a questa piattaforma di real-time process monitoring, Fedrigoni è riuscita a monitorare la resa produttiva dei suoi macchinari e identificare le ottimizzazioni su cui concentrarsi per sostenere l’efficienza produttiva per garantire un miglioramento della produzione anno su anno.
Su 7 impianti e 13 macchine coinvolte nel progetto, l’andamento della performance ha mostrato un +1,88% anno-su-anno di superamento del target dell’OEE negli ultimi tre anni e la riduzione del tempo di fermo di oltre 1 punto percentuale a fronte di un tempo di produzione più che raddoppiato.
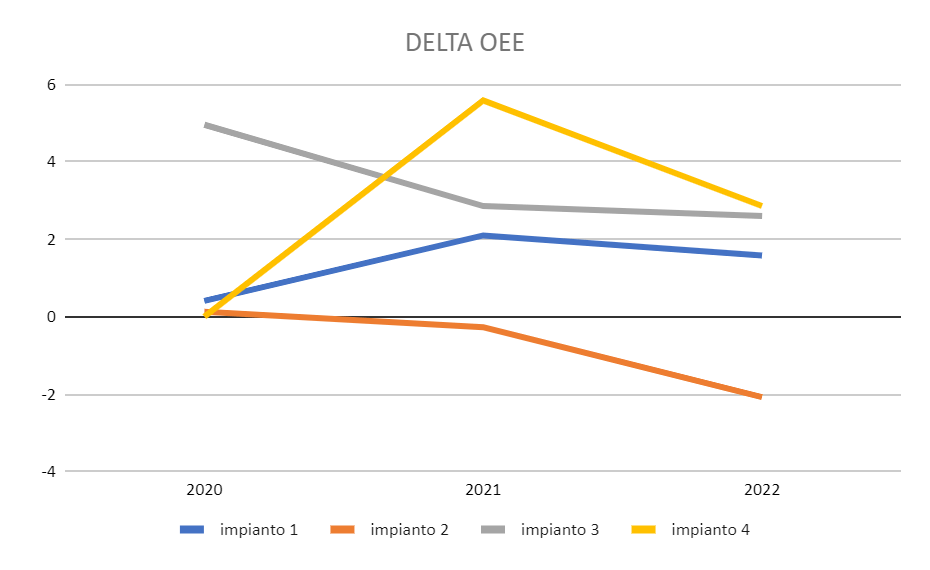
Fedrigoni è un esempio lampante di come anche produzioni già performanti possano ulteriormente ridurre gli scarti e migliorare i loro risultati attraverso analisi costanti dei dati di processo.
Si tende, quando ci troviamo di fronte a aziende di grandi dimensioni come Fedrigoni a ritenerli casi non riproducibili. Ma prodotti e framework di Data science sono stati pensati e strutturati proprio per standardizzare strumenti e buone pratiche, che permettono anche alle piccole e medie imprese del nostro prezioso manifatturiero italiano di investire in digitalizzazione con costi accessibili.
È fondamentale oggi, per poter realmente ottimizzare i nostri investimenti, costi ed emissioni, saper fare scelte fact-based nella gestione dell’azienda, sfruttando analisi affidabili dei nostri dati reali.